Introduction
Physical Vapor Deposition (PVD) is a critical technique used extensively in the manufacturing industry to enhance the surface properties of materials. This process involves the deposition of thin films of material onto various substrates, which can include metals, glass, ceramics, and plastics. PVD is celebrated for its ability to significantly improve the hardness, wear resistance, and corrosion resistance of coated products.
PVD’s relevance spans numerous industries including electronics, automotive, medical devices, cutting tools, and decorative products. Each application benefits from the unique properties imparted by the PVD coatings, such as improved longevity, enhanced performance, and aesthetic qualities. Additionally, PVD is a preferred method in these sectors due to its environmentally friendly nature, producing minimal hazardous waste compared to traditional chemical deposition processes.
By understanding the different PVD methods—such as sputtering, ion plating, and thermal evaporation—engineers and designers can select the most appropriate techniques for their specific needs, optimizing product performance and durability. This article will delve into the main types of PVD, highlighting their principles, applications, and the advantages they offer in industrial applications.
1. Vacuum Evaporation
Vacuum evaporation is a foundational PVD technique where materials (referred to as the evaporating material) are heated in a vacuum to the point where they evaporate and then condense on a target substrate to form a thin film. This method is particularly effective with a wide range of materials including metals, alloys, and organic compounds.
Process Description: In vacuum evaporation, material from a thermal source such as a tungsten filament or electron beam is heated until it vaporizes. The vapor travels through a vacuum chamber and deposits onto a cooler substrate, forming a uniform thin film. This process benefits from the low pressure environment of the vacuum, which reduces the presence of contaminants and allows for a cleaner deposition.
Common Materials: Metals like aluminum, gold, and silver; dielectric materials; and organic semiconductors are commonly used. These materials can be effectively vaporized and deposited to create functional and decorative coatings.
Key Applications: Vacuum evaporation is integral in the fabrication of microelectronics, where it is used to form contacts and interconnects in devices. It is also used to deposit thin film resistors and dielectric layers in capacitors, demonstrating its versatility and precision in creating components with specific electrical properties.
Advantages Over Other Methods: Vacuum evaporation allows for high-purity films with excellent thickness control. It is a relatively simple and fast process that requires lower temperatures compared to other PVD methods, making it ideal for temperature-sensitive substrates. The equipment is generally less complex and more cost-effective, especially for small-scale productions or research applications.
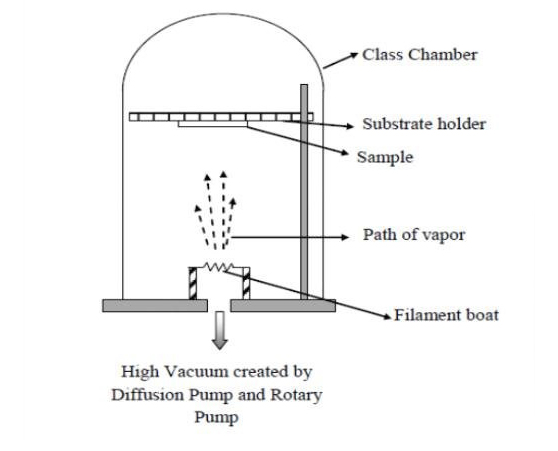
2. Sputtering Deposition
Sputtering deposition is a highly versatile PVD method that involves ejecting material from a target (or “sputter target“) through bombardment with energetic particles, usually ions, which then deposit onto a substrate to form a thin film. This method can be adapted to deposit a wide range of materials including metals, ceramics, and plastics.
Process Description: In sputtering, a target material is placed in a vacuum chamber opposite to the substrate. Ions generated in the plasma within the chamber are accelerated towards the target with enough energy to dislodge atoms. These atoms then travel through the vacuum and coat the substrate, forming a thin film. The process can be controlled to tailor film thickness and composition very precisely.
Varieties of Sputtering:
- Magnetron Sputtering: Utilizes magnetic fields to confine plasma close to the target surface, enhancing the efficiency of the ion bombardment and allowing for faster deposition rates.
- RF Sputtering (Radio Frequency Sputtering): Effective for insulating materials by using alternating current, thus avoiding charge build-up on the target.
- DC Sputtering (Direct Current Sputtering): Suitable for conductive materials, providing a steady ion stream.
- Ion-Beam Sputtering: Employs an ion beam directed at the target, allowing for more precise control over the deposition.
- Reactive Sputtering: Involves a reactive gas in the sputtering process, which forms a compound with the target material upon deposition.
Applications: Sputtering is commonly used to apply reflective coatings on glass, produce thin films for solar cells, and fabricate layers on semiconductor wafers. Its ability to coat complex shapes and features makes it invaluable in manufacturing electronics and display panels.
Benefits: This technique offers excellent control over film composition and thickness, making it possible to achieve specific electrical, optical, and mechanical properties. Sputtering can also cover large areas uniformly and is scalable from small research samples to large industrial components.
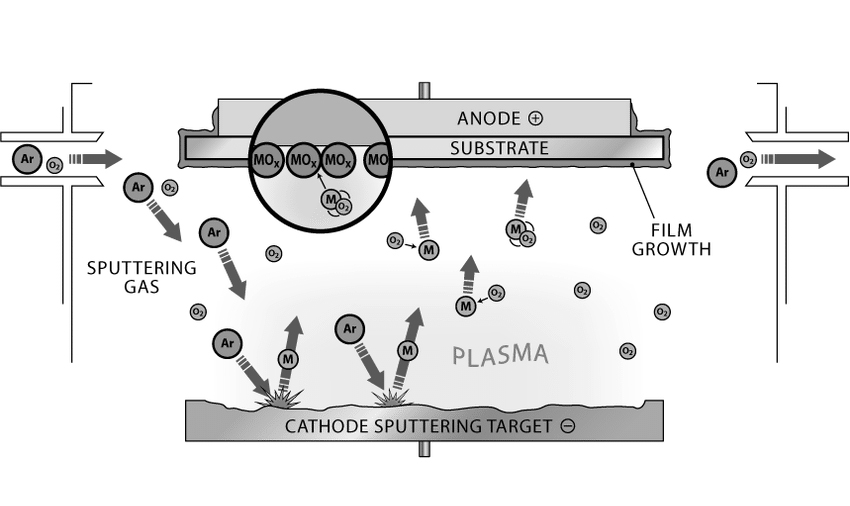
3. Plasma Spray Coating
Plasma spray coating is a PVD technique that utilizes a high-temperature plasma jet to melt and propel materials onto a substrate, forming a coating. This method is particularly effective for applying thick coatings over large surface areas and is highly versatile in terms of the materials it can process.
Process Description: In plasma spraying, a material in powder form is fed into a plasma torch, where it is rapidly heated to a molten or semi-molten state. The high-velocity plasma jet then propels these particles onto a substrate, where they flatten and rapidly cool to form a dense, strong coating. The process is conducted in a controlled atmosphere or under vacuum to prevent oxidation and ensure high-quality coatings.
Types of Materials: Metals, ceramics, plastics, and composites can all be plasma sprayed, making this technique suitable for a wide range of applications. The choice of material depends on the desired properties of the coating, such as thermal resistance, electrical conductivity, or biocompatibility.
Industrial Uses: Plasma spraying is extensively used in the aerospace industry for thermal barrier coatings on turbine blades and engine components, which helps in withstanding high temperatures and reducing wear. It is also popular in the biomedical field for coating medical implants to improve their integration with bone and other tissues.
Advantages: One of the primary advantages of plasma spray coating is its high deposition rates, which make it ideal for covering large areas quickly. The process also allows for the deposition of very thick coatings, which is beneficial for applications requiring robust wear and corrosion protection.
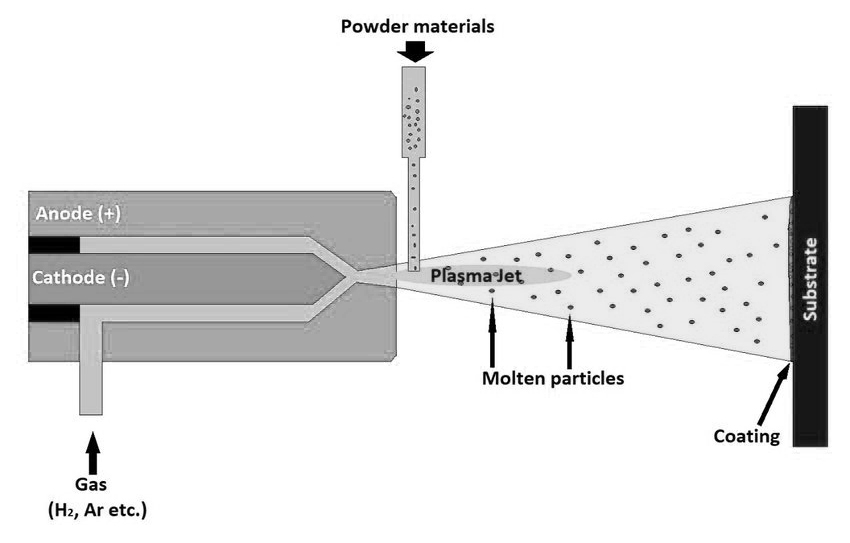
4. Ion Plating
Ion plating is a sophisticated PVD technique that enhances the adhesion and quality of thin films through the use of ionized vapor particles, which are accelerated towards the substrate under an electric field. This method is renowned for producing highly durable and adherent coatings, making it ideal for both functional and decorative applications.
Process Description: Ion plating involves evaporating the coating material, typically metals or alloys, in a vacuum chamber and then ionizing these vaporized particles using a plasma source. An electric field accelerates these ions towards the substrate, where they condense to form a thin film. This ion bombardment not only deposits the material but also increases the density and adhesion of the film through a process called “ion etching” that occurs simultaneously.
Common Materials: Materials frequently used in ion plating include titanium nitride (TiN), chromium, gold, and copper, each chosen for specific properties such as hardness, wear resistance, or aesthetic appeal.
Applications: Due to its strong film adhesion and versatility, ion plating is used extensively in the tool industry to extend the life of cutting and forming tools. It is also prevalent in the automotive sector for decorative trims and functional coatings that require enhanced durability. Additionally, the medical industry utilizes ion plating for surgical instruments and implants to improve biocompatibility and resistance to wear.
Advantages Over Other Methods: Ion plating is particularly noted for its superior film density and strong adhesion, which significantly improve wear and corrosion resistance. The method also allows for the coating of complex geometries and fine details, making it suitable for intricate designs and applications where precision is crucial.
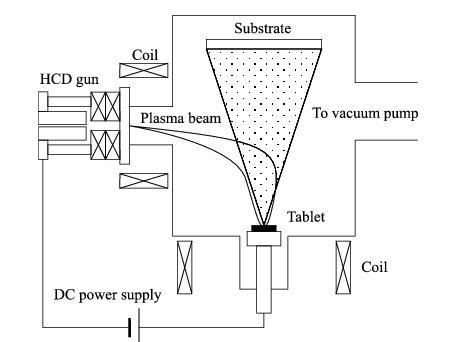
5. Cathodic Arc Deposition
Cathodic arc deposition, often referred to as arc PVD, is a method characterized by its ability to evaporate target materials through the use of an electric arc. This method excels in producing highly ionized vapor, which results in coatings that are extremely dense and adherent.
Process Description: The process involves striking an electric arc directly onto a material source or “target”, which rapidly heats and vaporizes the material in a highly ionized plasma form. This plasma is then condensed onto the substrate to form a coating. The high degree of ionization (ranging from 30% to 100%) enhances the film’s mechanical properties and adhesion to the substrate.
Common Materials: Commonly used materials in cathodic arc deposition include titanium, chromium, and zirconium, which are ideal for creating hard, wear-resistant coatings.
Applications: Cathodic arc deposition is predominantly used for tool coatings in industries requiring high durability and resistance to wear, such as cutting tools and dies. It is also used for decorative coatings in the automotive and architectural sectors due to the excellent finish and color consistency it provides.
Advantages Over Other Methods: The method’s ability to achieve high ionization levels makes the coatings more uniform and dense, which significantly improves their hardness and wear resistance. It also allows for better control over the chemical composition and microstructure of the coatings, leading to superior performance characteristics.
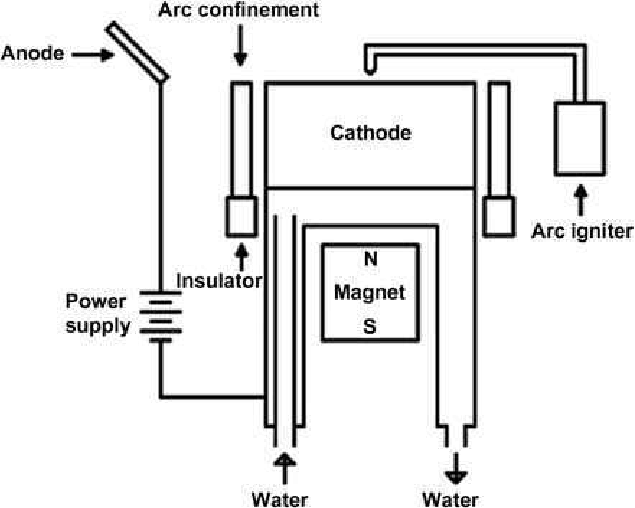
6. Pulsed Laser Deposition
Pulsed Laser Deposition (PLD) is a versatile PVD method that uses high-power laser pulses to vaporize material from a target, which then deposits on a substrate to form a thin film. This method is particularly favored for its ability to deposit a wide range of materials with precise control over the film’s composition and thickness.
Process Description: In PLD, a laser beam is directed at the target material in a vacuum chamber. The intense energy of the laser pulse vaporizes the surface of the target into a plasma plume, which then deposits on the substrate. The process allows for the deposition of materials with complex stoichiometries and high melting points.
Common Materials: PLD can be used with materials that are challenging to deposit by other methods, including high-temperature superconductors, complex oxides, and thin films for photovoltaics.
Applications: Due to its precise control over material deposition, PLD is extensively used in the electronics industry for developing advanced thin films in semiconductors and solar cells. It is also used in research environments for developing new material layers with unique properties.
Advantages Over Other Methods: PLD stands out for its ability to maintain the exact composition of the target material in the deposited film, which is crucial for functional materials in electronic and optical applications. The method also allows for rapid prototyping of multi-layer and multi-material structures, providing flexibility in research and development settings.
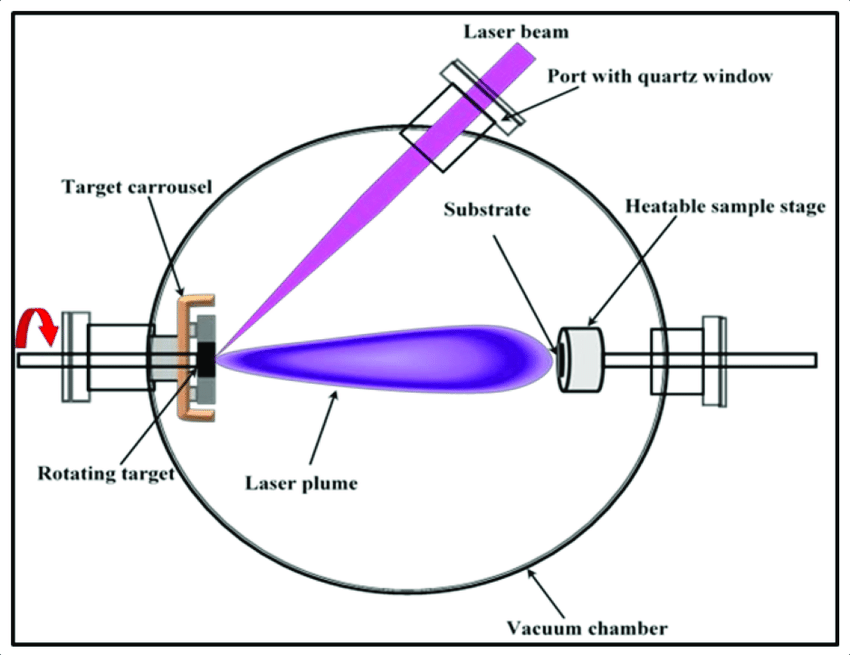
7. Electron Beam Physical Vapor Deposition
Electron Beam Physical Vapor Deposition (EBPVD) is a specialized PVD technique that uses an electron beam to heat and vaporize the target material in a vacuum, resulting in high-quality, pure thin films. This method is particularly effective for materials with high melting points and for applications requiring precise control over film properties.
Process Description: In EBPVD, an intense beam of electrons is focused on the target material, causing it to heat and eventually vaporize. The vaporized material then travels across the vacuum chamber and condenses on the substrate, forming a thin film. The process is conducted under high vacuum conditions, which minimizes contamination and allows for the deposition of very pure materials.
Common Materials: High-melting-point metals such as tungsten, molybdenum, and compounds like titanium nitrides are commonly used. These materials benefit from the high energy input of the electron beam, which can efficiently vaporize them despite their high melting temperatures.
Applications: EBPVD is widely used in the aerospace industry for coating turbine blades with thermal barrier coatings to enhance their durability and performance at high temperatures. It is also used in the semiconductor industry for depositing films with high electrical conductivity and in optical applications for anti-reflective coatings.
Advantages Over Other Methods: EBPVD offers several advantages, including high deposition rates and the ability to deposit extremely pure and dense films. It is particularly well-suited for applications requiring films with precise thickness and uniformity over large areas.
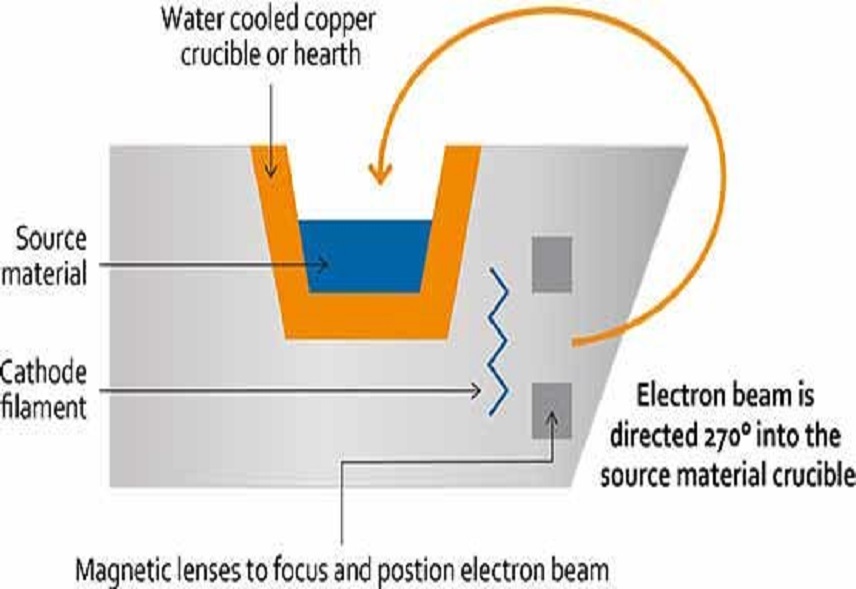
Comparative Analysis
Efficiency and Cost:
- Vacuum Evaporation is noted for its simplicity and cost-effectiveness, particularly suitable for small-scale operations and research environments.
- Sputtering Deposition offers high efficiency in material utilization and is versatile but tends to be more expensive due to the complexity of the equipment.
- Ion Plating provides superior coating quality and durability but at a higher operational cost and energy consumption.
- Plasma Spray Coating excels in depositing coatings rapidly over large areas, making it cost-effective for large-scale applications despite high initial setup costs.
- Cathodic Arc Deposition is highly efficient in terms of deposition rate and material utilization but may require significant maintenance due to electrode wear.
- Pulsed Laser Deposition allows for extremely precise control over film properties but involves high costs associated with laser equipment.
- Electron Beam Physical Vapor Deposition offers high deposition rates and can handle high-melting-point materials efficiently, though the cost of electron beam equipment is substantial.
Material Suitability:
- Each method has specific advantages depending on the material. For instance, Ion Plating and Cathodic Arc Deposition are preferred for metals and hard coatings, while Pulsed Laser Deposition is ideal for complex oxides and precision applications.
Typical Applications:
- Sputtering and Ion Plating are commonly used in the electronics industry for their precision and quality.
- Plasma Spray Coating is favored in aerospace for thermal barriers and in the medical field for implant coatings.
- Electron Beam Physical Vapor Deposition is indispensable in aerospace for thermal and barrier coatings due to its ability to handle very high temperatures.
Decision Factors:
- Selecting a PVD method involves balancing cost, efficiency, material properties, and the specific industrial application. Factors such as substrate compatibility, desired film characteristics, production volume, and environmental considerations also play crucial roles.
Table 1: Comparative Analysis of Physical Vapor Deposition (PVD) Methods
PVD Method | Efficiency and Cost | Material Suitability | Typical Applications | Key Decision Factors |
---|---|---|---|---|
Vacuum Evaporation | Noted for simplicity and cost-effectiveness; ideal for small-scale operations and research. | Suitable for a wide range of materials including metals and organics. | Microelectronics, thin film resistors, dielectrics. | Cost, simplicity, research and development focus. |
Sputtering Deposition | High material utilization but more expensive due to equipment complexity. | Versatile; works with metals, ceramics, and polymers. | Electronics, coatings for glass, and solar panels. | Efficiency, material versatility, equipment cost. |
Ion Plating | Superior coating quality at higher operational costs and energy consumption. | Preferred for metals and hard coatings. | Decorative applications, tool coatings, automotive parts. | Coating durability, quality, energy considerations. |
Plasma Spray Coating | Rapid deposition over large areas; cost-effective for large-scale applications despite high setup costs. | Works with metals, ceramics, plastics, composites. | Aerospace (thermal barriers), medical implants. | Scale of application, coating thickness, substrate compatibility. |
Cathodic Arc Deposition | Highly efficient in deposition rate and material utilization; maintenance can be high due to electrode wear. | Ideal for hard, wear-resistant coatings. | Tool coatings, decorative finishes. | Maintenance, efficiency, deposition rate. |
Pulsed Laser Deposition | Precise control over film properties; high costs associated with laser equipment. | Best for complex oxides and precision applications. | Advanced electronics, photovoltaics, research applications. | Precision, cost of equipment, research focus. |
Electron Beam Physical Vapor Deposition | High deposition rates; efficient with high-melting-point materials but costly equipment. | Effective for very high temperature applications. | Aerospace (thermal and barrier coatings), optical coatings. | High temperature capabilities, equipment cost, deposition rates. |
Conclusion
Throughout this article, we have explored the diverse array of Physical Vapor Deposition (PVD) methods, each offering unique benefits and suited for specific industrial applications. From the simplicity and cost-effectiveness of vacuum evaporation to the advanced capabilities of pulsed laser deposition, PVD technologies provide critical solutions across sectors including electronics, aerospace, automotive, and medical industries.
The key advantages of PVD, such as improved durability, enhanced performance characteristics, and environmental sustainability, make it an invaluable process in modern manufacturing. Its ability to apply coatings that are thin yet robust allows for significant advancements in material science and engineering, pushing the boundaries of what is possible in wear resistance, thermal insulation, and aesthetic finishes.
As we look to the future, the role of PVD is set to expand further. The ongoing development of hybrid techniques, greater automation, and nanostructured coatings are poised to enhance the efficiency and effectiveness of PVD methods. Moreover, the increasing focus on sustainability and the rising demand in emerging markets highlight the growing importance of PVD technologies globally.
Highlighting industry participation, Stanford Advanced Materials (SAM) is a global supplier of various PVD coating materials such as metals, alloys, oxides, ceramics, etc. We provide sputtering targets and evaporation materials for a wide range of applications from ferromagnetic, complex oxides, and semiconducting films. SAM’s contributions underscore the widespread industrial use and adaptability of PVD technologies.
In conclusion, Physical Vapor Deposition stands as a cornerstone of advanced manufacturing, continually evolving to meet the challenges of a rapidly changing technological landscape. For those interested in further exploring this field, additional resources and links provided in this article offer avenues for deeper understanding and engagement with the latest in PVD research and applications.