Introduction
Plasma spray coating is a form of thermal spraying. It involves heating a material electrically and spraying it on the substrate to be coated. This process can be used on a large surface area at a higher deposition rate than most other methods of thin-film deposition. A wide range of materials can be used for plasma spray coating, including metals, plastics, ceramics, alloys, and composites. They are usually fed in powder form and heated until they get to a molten state. In the molten state, these materials are sprayed on the substrate.
Process
Plasma spray coating is a complex and highly regulated process. The material that is deposited on the substrate in plasma spray coating is commonly called the feedstock. In plasma spray coating, the feedstock is put into a plasma jet with a temperature of about 10000 K. Once in the plasma jet, the feedstock is melted into a molten form. The plasma jet then propels the material onto the surface of the substrate. The molten material solidifies and forms a coating on the substrate.
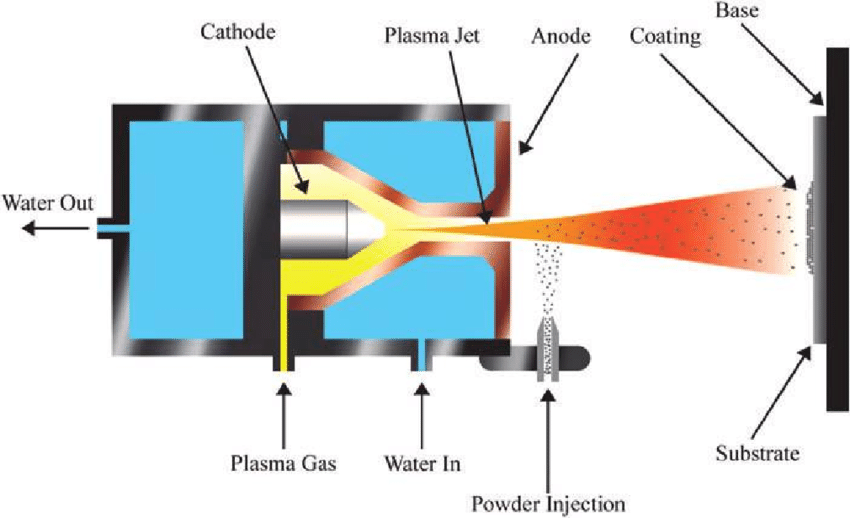
Properties of Plasma Spray Coating
When discussing the properties of plasma spray coating, there are four factors to consider. These factors are structure, porosity, the strength of adhesion, and surface quality.
Structure
The spray particles used for plasma spray coating usually exist in a spherical form. This minimizes surface tension. When the spray particles are deposited on the substrate, they spread out and assume a laminate form.
Porosity
This is another important factor to consider when discussing the properties of plasma spray coating. Different plasma spray coating processes give rise to products with different porosity. Some processes may give rise to porosity of less than 1 % while others might give rise to a much larger porosity. To control porosity one may use a very coarse spray powder.
Strength of Adhesion
The strength of adhesion in plasma spray coating increases when the surface of the substrate is rough. Using surface blast to roughen the surface of the substrate can improve the strength of adhesion. In addition, removing rust from the surface of the substrate can also improve the strength of adhesion.
Surface Quality
Thin coatings of up to 0.5mm from plasma spray coatings can protect the surface of a substrate sufficiently. High residual stress can result from thick coatings and this should be carefully avoided.
Advantages of Plasma Spray Coating
Plasma spray coating has interesting advantages that make it popular in various industries. Let us look at some of them below.
- Plasma spray coating can use a wide range of coating materials. This means the process can be used for products that have a wide range of uses.
- Plasma spraying can be used for a wide range of substrates such as ceramics, metals, plastics, and glass.
- Plasma spray coating is suitable for coating refractory tools. This is due to the high temperature of the plasma jet.
- This process can be used on temperature-sensitive substrates without damaging the substrates. This is because the process involves minimal heating of the substrate.
Disadvantages of Plasma Spray Coating
- It is not ideal for substrates with complex geometry. This is because it is a line of sight process and may not be able to coat such substrates completely.
- The equipment used for this process is high maintenance. The internal components of the plasma spray gun deteriorate occasionally.
- It is a relatively expensive process. Plasma spray coating costs a lot more than other types of thermal spraying.
- Plasma spray coating is a complex process. Therefore, it requires a high level of technical know-how.
Applications of Plasma Spray Coating
Aerospace
Plasma spray coating can be used to coat aircraft turbines. A wide range of materials can be deposited through this process to meet the requirements of the aircraft.
Electronics
Semiconductors used in making internal components of electronics are coated by plasma spray coating. Plasma spray coating is also used to coat the exterior of electronics such as hairdryers.
Medicine
In medicine, plasma spray coating is used to coat some dental and medical implants. In addition, some surgical tools are coated by plasma spray coating.
Other Types of Thermal Spray Coating
There exist other types of thermal spray coating asides from plasma spray coating. Some of these types are more similar to plasma spray coating than others.
Electric Arc Spraying
This involves two wires that are arranged to form an arc. The feedstock melts at the point where the two wires meet.
High-Velocity Oxy-Fuel Spraying (HVOF)
This type of thermal spraying is not ideal for high temperatures. However, its products have a higher resistance to corrosion than products of plasma spray coating.
Conclusion
Plasma spray coating is an asset to various industries across the world. Its durability and versatility make it one of the most popular methods of thermal spraying. For more information about thin film coating, please visit https://www.sputtertargets.net/.