Introduction
Chemical vapor deposition is a coating method that is commonly used to produce thin films and coatings of very high quality. Gaseous reactants are usually used in this process. In chemical vapor deposition, you transport one or more volatile precursors to the reaction chamber. The volatile precursors usually decompose on a heated substrate surface in the reaction chamber. This process creates some chemical by-products which are emitted from the reaction chamber alongside the unreacted volatile precursors. A lot of materials are deposited via the chemical vapor deposition method, including silicides, metal oxides, sulfides, and arsenides.
Here is a QUICK GUIDE for this article:
1. Two Chemical Vapor Deposition Reactors
2. Types of Chemical Vapor Deposition Processes
- Plasma-enhanced Chemical Vapor Deposition (PECVD)
- Thermal Chemical Vapor Deposition (Thermal CVD)
- Hot-filament Chemical Vapor Deposition (HFCVD)
- Metalorganic Chemical Vapor Deposition (MOCVD)
- Laser Chemical Vapor Deposition (LCVD)
3. Benefits of Chemical Vapor Deposition
4. Applications of Chemical Vapor Deposition
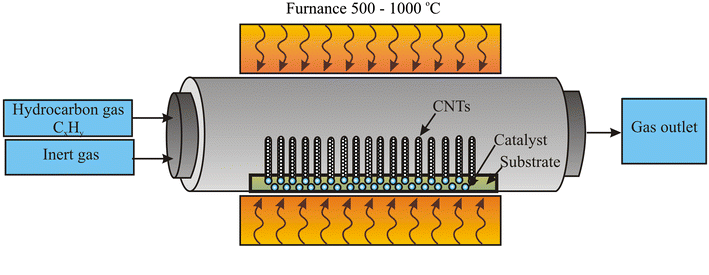
Two Chemical Vapor Deposition Reactors
There are two types of CVD reactors, each with its own applications, advantages, and disadvantages.
Hot Wall Reactors
Hot wall reactors are less commonly used compared to other types. They involve heating both the substrates and the reactor walls.
Advantages
- Large batches of substrates can be produced at once.
- Hot wall reactors are easy to operate.
- There is a uniform substrate temperature. Hence, there is a uniform coating thickness.
- Hot wall reactors can operate at a wide range of temperatures and pressures.
Disadvantages
- It requires a very high temperature and energy.
- Coating occurs not only on the substrate but also on the reactor walls. This makes it difficult to clean the reactor.
- Gas-phase reactions are likely to occur.
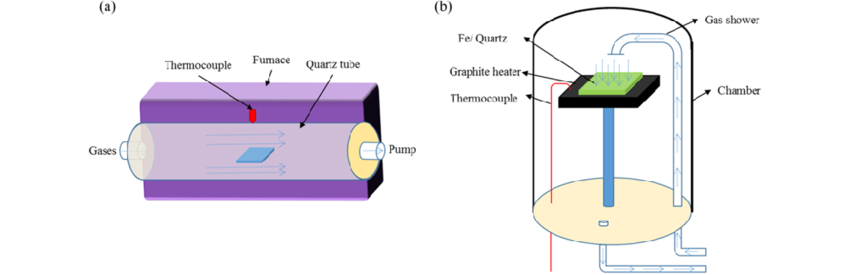
Cold Wall Reactors
Cold wall reactors are the most commonly used type of CVD reactor. They heat the substrate while cooling the reactor walls. This creates a higher temperature on the substrate compared to the walls. Cold wall reactors are particularly suitable for compound semiconductor CVD processes.
Advantages
- There are fewer coatings on the walls, making cleaning easier.
- Cold wall reactors require less temperature and energy.
- Cold wall reactors support chemical vapor deposition processes that involve plasmas.
- Depositions occur at a faster rate.
- Gas-phase reactions are less likely to occur.
Disadvantages
- They are more difficult to operate.
- Fewer substrates can be worked on at once.
- The substrate temperature is not uniform. Hence coating thickness is usually not uniform.
Types of Chemical Vapor Deposition Processes
Plasma-enhanced Chemical Vapor Deposition (PECVD)
PECVD is a specialized form of chemical vapor deposition. In this method, the reactive gases are ionized into plasma using a combination of radio frequency or direct current discharge. This ionization process occurs within the space between two electrodes, where the gases are introduced and transformed into plasma. This technique enhances the deposition process by allowing the films to be deposited at lower temperatures compared to standard CVD methods.
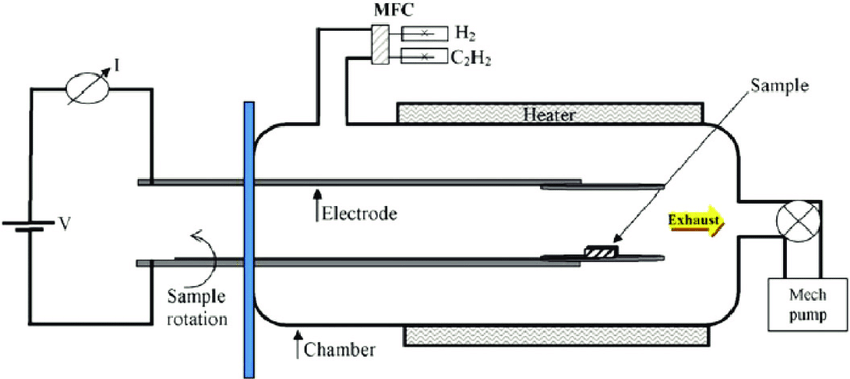
Thermal Chemical Vapor Deposition
In Thermal CVD, coatings are easily deposited on the substrates in the open atmosphere. In this process, the precursor material is added to burning gas, making the precursor highly reactive. This method facilitates the deposition of thin films directly onto substrates at atmospheric pressure, utilizing the enhanced reactivity of the precursors facilitated by the heat from the burning gas to achieve efficient and uniform coatings.

Hot-filament Chemical Vapor Deposition (HFCVD)
HFCVD, also known as catalytic chemical vapor deposition, utilizes a heated filament to decompose precursor gases. In this process, the hot filament serves as a catalyst, significantly enhancing the breakdown of the gases. Positioned above the substrate, which is maintained at a lower temperature compared to the filament, this method ensures efficient deposition of materials onto the substrate. The differential temperature between the hot filament and the cooler substrate facilitates a controlled deposition environment, leading to uniform and high-quality coatings.
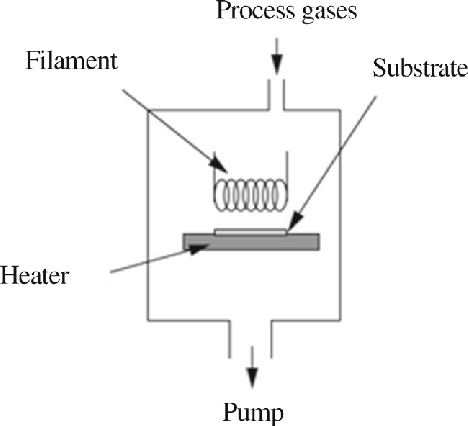
Metalorganic Chemical Vapor Deposition (MOCVD)
MOCVD is a specialized technique extensively used for depositing single or polycrystalline thin films. Unlike molecular beam epitaxy, which involves physical deposition to grow crystals, MOCVD operates through chemical reactions. In this process, precursors such as germane, phosphine, and ammonia are typically used. These chemical compounds undergo decomposition under controlled conditions, leading to the formation of thin film materials on substrates. This distinction emphasizes MOCVD’s role in facilitating complex chemical transformations essential for the production of advanced material coatings.
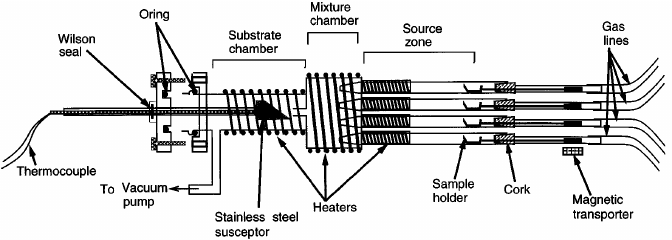
Laser Chemical Vapor Deposition (LCVD)
LCVD is a precise method commonly utilized for spot coating applications, especially in the semiconductor industry. This technique employs a focused laser beam to selectively heat specific areas of a substrate. The localized heating by the laser accelerates the deposition process on the heated areas, allowing for rapid and controlled growth of material coatings. This targeted approach ensures high precision in coating placement and thickness, making LCVD ideal for applications requiring meticulous material deposition on complex substrate geometries.
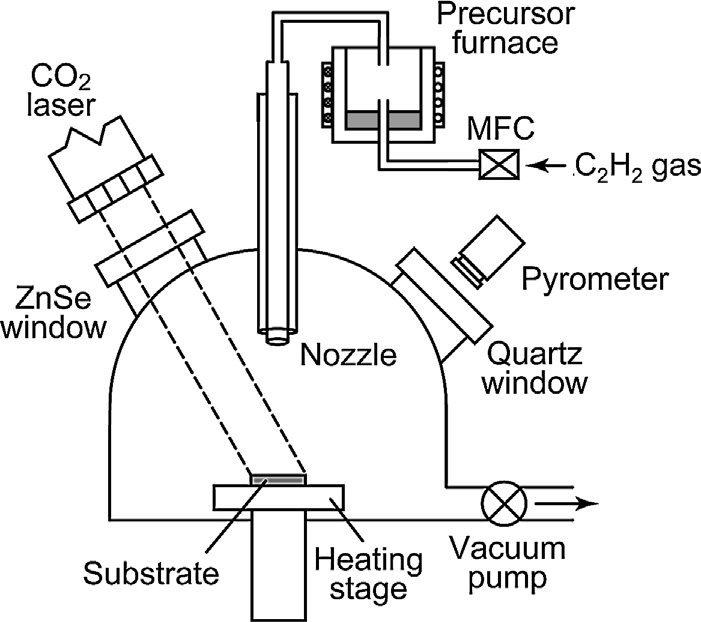
Yu, Shu & Tu, Rong & Goto, Takashi. (2015). Preparation of SiOC nanocomposite films by laser chemical vapor deposition. Journal of the European Ceramic Society. 36. 10.1016/j.jeurceramsoc.2015.10.029.
Benefits of Chemical Vapor Deposition
Chemical Vapor Deposition (CVD) is a widely used method for applying thin films to surfaces, and its popularity stems from several key advantages that make it suitable for various industrial applications. Here are some expanded insights into the benefits of using CVD:
- Affordability: CVD is recognized for being a cost-effective coating method compared to other deposition techniques. Its efficiency and ability to operate at scale reduce overall manufacturing costs, making it an economically viable option for both high-volume production and specialized applications where cost containment is crucial.
- Versatility: One of the standout features of CVD is its versatility. This method is capable of depositing a wide range of materials, including metals, ceramics, and polymers, onto virtually any substrate. This flexibility makes it invaluable in industries ranging from aerospace to electronics, where it is used for depositing everything from protective coatings to conductive layers.
- High Deposition Rate: CVD processes are particularly noted for their high deposition rates, enabling rapid coating of substrates which is a significant advantage in mass production settings. This efficiency ensures that large batches of components can be processed quickly, enhancing throughput and reducing turnaround times.
- Uniform Coating: The ability to provide a consistent, uniform coating over the entire surface of a substrate, including complex geometries and varying scales, is another benefit of CVD. This uniformity is critical in applications where the precise thickness of a coating influences the performance or durability of the end product, such as in semiconductor manufacturing or protective coatings in aerospace components.
- High Purity: Chemical vapor-deposited materials are typically of very high purity, as the process involves the deposition of vapor-phase precursors that can be carefully controlled and purified before use. This results in coatings free from impurities that could compromise the structural integrity or functionality of the coating.
- Non-Line of Sight Deposition: Unlike line-of-sight processes, CVD can coat complex shapes and internal surfaces that are not directly exposed to the source of the deposition material. This capability is particularly important for components with intricate designs or internal cavities that require consistent coverage, such as parts used in fluid flow systems or complex electronic devices.
Further Reading: Table Comparison: Physical Vapor Deposition Vs. Chemical Vapor Deposition
Applications of Chemical Vapor Deposition
Electronics
In the realm of electronics, CVD plays a pivotal role in semiconductor fabrication, where it is employed to deposit thin films that are essential for the manufacturing of integrated circuits and transistors. These thin films form the active layers and gate dielectrics crucial for the function of electronic devices. The ability of CVD to create uniform and defect-free layers with high precision makes it indispensable in producing the increasingly miniaturized components required for advanced electronics.
Further Reading: CVD Technology’s Impact on Semiconductor Thin Film Production
Cutting Tools
Chemical vapor deposition is extensively used in the tool-making industry to coat cutting tools, such as drills and milling cutters. The CVD coatings, typically made from materials like titanium nitride or diamond-like carbon, significantly enhance the durability, efficiency, and performance of these tools. These coatings reduce tool wear and corrosion, improve lubricity to reduce friction, and provide a thermal barrier that helps in maintaining the tool’s integrity under high-heat conditions. This leads to longer tool life, greater precision in machining, and reduced downtime for tool replacement.
Solar Cells
The manufacture of thin-film solar cells is another prominent application of CVD. This process involves the deposition of one or more layers of photovoltaic materials onto a substrate. These materials can include silicon, cadmium telluride, or copper indium gallium selenide, each offering different efficiencies and characteristics. CVD is critical in this context because it allows for the precise control over the thickness and composition of the deposited layers, which is vital for optimizing the performance and efficiency of the solar cells. As the demand for renewable energy solutions increases, the role of CVD in enabling cost-effective and high-efficiency solar panels becomes even more significant.