We have previously made a brief introduction of Five Sputter Coating Technologies, including unbalanced magnetron sputtering, radio frequency sputtering (RF sputtering), direct current magnetron sputtering (DC sputtering), mid-frequency alternating current magnetron sputtering (AC sputtering), and reactive magnetron sputtering. In this article, we are going to talk about direct current (DC) sputtering in detail.
To begin with, let’s see the definition of DC Sputtering. Direct Current Sputtering (DC Sputtering) is one of the Physical Vapor Deposition (PVD) Coating techniques. It uses a target material as the coating, which is bombarded with ionized gas molecules, causing atoms to be “sputtered” off into the plasma. Then, when these atoms condense as a thin film, they are deposited on the substrate to be coated.
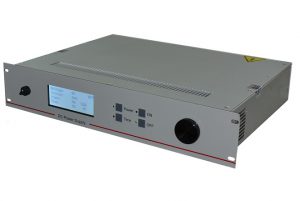
Advantages and Disadvantages of DC Sputtering
DC Sputtering is one of the most basic sputtering types for PVD metal deposition and electrically conductive target coating materials, because it is easy to control and it is inexpensive. Other features of magnetron sputtering technology include that the sputtering voltage is small, the sputtering rate is high, and the sputtering gas pressure is low (usually 0.5Pa). Due to the above advantages, DC sputtering is widely used in the semiconductor industry, jewelry industry, watch industry and others. It can be used for creating microchip circuitry, optical components as well as metalized packaging plastics.
Although DC Sputtering is a low-cost option if you are doing metal deposition for coating, it still has many limitations. Its main dilemma is that non-conducting dielectric insulating materials take on a charge over time that may bring about exceptional issues like arcing, or the poisoning of the target material with a charge that may completely stop the sputtering. To solve the problems brought by DC Sputtering, people begin to develop other sputter coating technologies, for instance, as we mentioned at the beginning, the Radio Frequency (RF) Sputtering. RF Sputtering alternates the electrical charge at radio frequency, thus it can prevent a charge accumulating on the target or coating material.
Difference Between DC Sputtering And RF Sputtering
DC Sputtering uses DC power supply, and RF Sputtering uses AC power supply (RF belongs to the category of AC, and the frequency is 13.56MHz. The frequency of our usual life electricity is 50Hz). DC magnetron sputtering is generally used for sputtering of conductive target, such as pure metal sputtering targets, and RF sputtering is generally used for sputtering of non-conductive targets, such as oxide ceramic sputter targets.
DC magnetron sputtering can only be applied to conductive targets, not limited to metals. For example, for an aluminum metal target, a non-conductive oxide film is easily formed on its surface, resulting in the accumulation of charges on the surface of the target (target poisoning), and in severe cases, DC sputtering cannot be performed. In this case, RF power is required. Simply put, when using the RF sputtering power supply, a small part of the time is the charge accumulated on the target, and target poisoning will not occur.
Related Reading: Sputter Coating Technologies: Radio Frequency Sputtering (RF Sputtering)
Conclusion
Thank you for reading our article and we hope it can help you better understand DC sputtering. If you want to know more about other sputtering methods, we would like to advise you to visit Stanford Advanced Materials (SAM) for more information. We regularly update knowledge and interesting stories about sputtering targets, and if you like this article, please share it with your friends.