Introduction
Vacuum evaporation is a process in which a solid material (referred to as the evaporating material) is heated in a high vacuum environment to be deposited on a specific substrate to obtain a film. The vacuum evaporation process is mainly used in microelectronics to make active components, device contacts, and metal interconnections, high precision low-temperature coefficient thin film resistors, and insulating dielectrics and electrodes for film capacitors.
Various Types of Evaporation Pellet Materials
The formation of various films by the vacuum evaporation process is an important technology for integrated circuit fabrication. A wide range of materials, such as conductive materials, dielectric materials, magnetic materials, and semiconductor materials, can be deposited by vacuum evaporation.
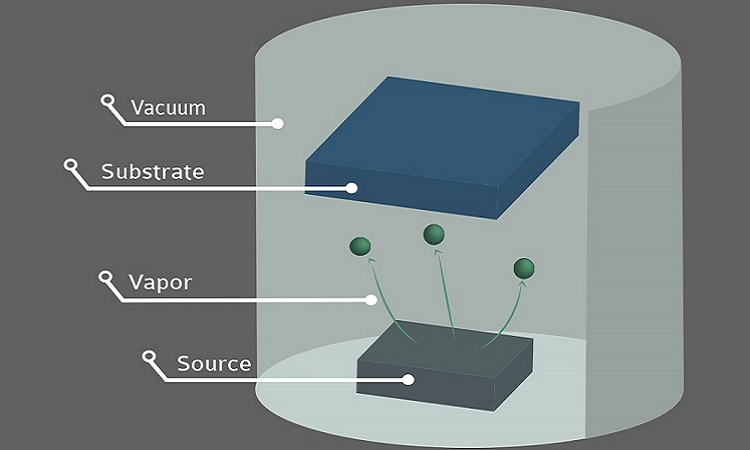
Vacuum Degree and Film Quality
In the vacuum evaporation process, the vacuum degree of the system directly affects the quality of the film. To deposit the evaporating atom or molecule on a substrate at a distance from the evaporation source, the vacuum of the vacuum chamber should generally be better than 6 x 10-2 Pa.
Heating Methods
In the vacuum chamber, the evaporation material is only evaporated when its vapor pressure is above 1 Pa. For this reason, it is often necessary to heat the evaporating pellets to 1000 to 2000 ° C; for some refractory materials, it has to be heated to as high as 3000 ° C.
There are two common heating methods:
1. Direct Heating: In this method, a high-melting-point conductor, such as a mixture of molybdenum, niobium, tungsten, or graphite, is fashioned into a basket or boat of various shapes. The evaporation pellets are placed on these conductors, and a high current is passed through them to elevate the temperature sufficiently for evaporation.
2. Indirect Heating: Some materials are prone to erosion when exposed to high temperatures directly, making direct heating unsuitable. In such cases, heat-resistant and stable materials like alumina, yttrium oxide, or zirconia are used to make a crucible. The evaporation material is placed inside the crucible, and the heater heats and evaporates the material through the crucible.
Evaporation Techniques
Various techniques can be employed during vacuum evaporation to achieve specific film characteristics. Some of these techniques include:
1. Electron Beam Evaporation: The electron beam is accelerated under an electric field of 5 to 10 kV/cm, and the electron beam is focused by an electron lens, and the temperature of the evaporation material in the crucible is raised to its evaporation temperature.
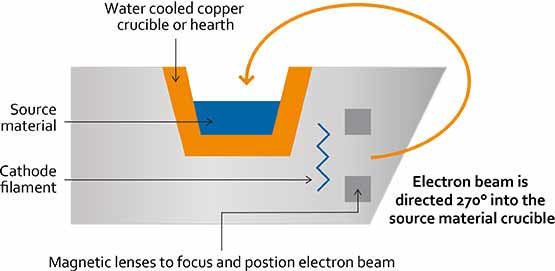
2. Multi-Source Evaporation: According to the composition of the film, the material is simultaneously heated and evaporated using two or more evaporation sources, and deposited on the same substrate. Different film compositions can be obtained by controlling the strength of each evaporation source.
3. Instant Evaporation: The multi-element material prepared as needed is placed in a specific container in the vacuum chamber. When the heater reaches the predetermined temperature, a certain amount of material is quickly sent to the heater that has reached high temperature through the feeding mechanism and is heated instantaneously to obtain a film of a certain composition.
4. Laser Evaporation: The surface of the evaporation material is irradiated with a laser pulse with a very high power density so that the exposed surface of the material is instantly heated to several thousand degrees. Any material will rapidly vaporize and evaporate at this high temperature.
5. Reaction Evaporation: While evaporating, a certain proportion of reactive gases (such as oxygen, nitrogen, etc.) is introduced into the vacuum chamber, and atoms of the evaporation material combine with the reaction gas during the deposition to form a compound film.
About SAM
SAM offers a variety of high-quality elemental and composite evaporation materials in a full range of purities and dimensions to suit any customer’s needs by the gram, kilogram, troy ounce, pound, pellet, and spool in any of our available purities. SAM also provides various evaporation sources for both thermal and e-beam evaporation, including metal and ceramic boats, filaments, crucibles and heaters, and e-beam crucible liners. Please visit https://www.sputtertargets.net/ for more information.