The yttrium oxide dielectric film refers to a thin film material as a dielectric, which is an important component and ideal material of a hybrid integrated circuit used in the electronics industry.
Yttrium Oxide Dielectric Film Properties
Y2O3 is a white powder with a crystal structure of body-centered cubic. Yttrium Oxide Dielectric Film has good thermal stability and large relative permittivity. The relative permittivity of a material is its (absolute) permittivity expressed as a ratio relative to the vacuum permittivity. It is also known as the rate of induction, which is related to frequency. The Y2O3 films prepared by different methods have different relative permittivity, 11 for electron beam evaporation, 17.1 for anodization, 11 for high frequency sputtering, and 15 for reactive sputtering.
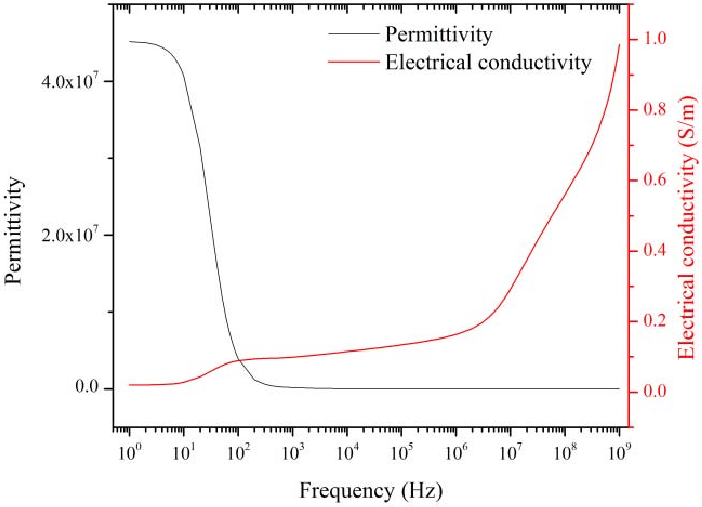
Yttrium Oxide Dielectric Film Preparation
As mentioned above, the preparation methods of the yttrium oxide dielectric film mainly include electron beam evaporation, anodization, high-frequency sputtering and reactive sputtering, and the latter two can be classified as sputter coating.
Electron beam evaporation: The electron beam evaporation is a method of vacuum evaporation coating, in which the evaporation material is directly heated and evaporated by an electron beam under vacuum to vaporize and it is then transported to a substrate to form a film on a substrate. The Y2O3 film prepared by electron beam evaporation method using yttrium oxide evaporation materials is a polycrystalline film;
Anodizing method: forming the Y2O3 film on the surface of the ruthenium film. If the substrate can be immersed in the electrolyte, the film forming speed is very fast (5 nm/s), and the prepared oxide film has excellent performance;
Reactive sputtering method: sputtering the Yttrium sputter target in a mixed gas of argon and oxygen, and the yttrium target would react with the gas to form the yttrium oxide. Reactive sputtering is suitable for the case where the chemical composition of the film and the target material are greatly different;
High-frequency sputtering method: The shape of the yttrium oxide sputtering target for high-frequency sputtering is circular or square, depending on the electrode structure of the sputtering apparatus, and the purity is 99.99%. The advantage of this method is that the loss angle and the temperature coefficient of the film are both small.
Yttrium Oxide Dielectric Film Application
Yttrium oxide is a thin film material acts as a dielectric, which is an electrical insulator that can be polarized by an applied electric field. When a dielectric is placed in an electric field, electric charges do not flow through the material as they do in an electrical conductor but only slightly shift from their average equilibrium positions causing dielectric polarization.
Y2O3 dielectric film can also be used to fabricate thin-film capacitors, which are 4 to 5 times larger than SiO capacitors. Capacitors are one of the most widely used electronic components in electronic devices, so Y2O3 capacitor film coating is critical in the electronics industry.
For more information, please visit https://www.sputtertargets.net/.