What is Hot Isostatic Pressing?
Hot isostatic pressing is one of the methods popularly used to process chemical materials. In this method, a material is compressed in a furnace at temperatures between 1173 K to 2523 K and pressures between 100 to 200 MPa. It is quite similar to another process known as hot pressing. During hot isostatic pressing, the gas pressure is uniformly distributed in all directions of the material. This ensures that the properties in different directions of the material are equal. Over the years, HIP has gained popularity for its efficiency. It is used to densify metal powders and remove defects in solid materials. Some of the defects that may be removed by this process include pores, voids, and cracks.
Further Reading: An Introduction to Cold Isostatic Pressing (CIP)
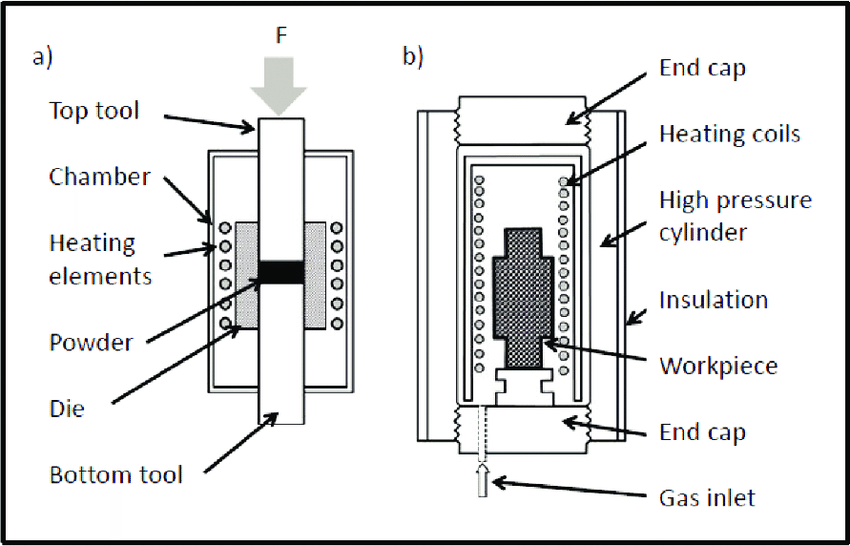
Advantages of Hot Isostatic Pressing
Uniform strength
With hot isostatic pressing, there is uniform strength in all directions of the material. This is because the pressure used in the process is applied equally in all directions of the material.
Mechanical Properties
Materials that undergo hot Isostatic processing have improved mechanical properties. These properties include ductility and strength. The improvement in mechanical properties can be attributed to the fact that most defects in the material are eliminated during HIP.
Corrosion Resistance
Hot isostatic pressing improves corrosion resistance. This ensures that materials that undergo HIP have an extended lifespan than most other materials.
Cost Effectiveness
HIP is a highly cost-effective process. With this process, less money is spent on quality assurance tests. This is because the materials that undergo hot isostatic processing have high quality. In addition, the extended lifespan the process confers on a solid material means that the material can be used for a long time before it is replaced.
Microstructure
There is a greatly improved microstructure for materials that undergo hot isostatic pressing. The microstructure of these materials is homogeneous. Also, the grains are fine and unsegregated.
Factors that Determine the Degree of Densification in HIP
The degree of densification that occurs via hot isostatic pressing varies from one material to the other. Three factors determine the degree of densification in this process.
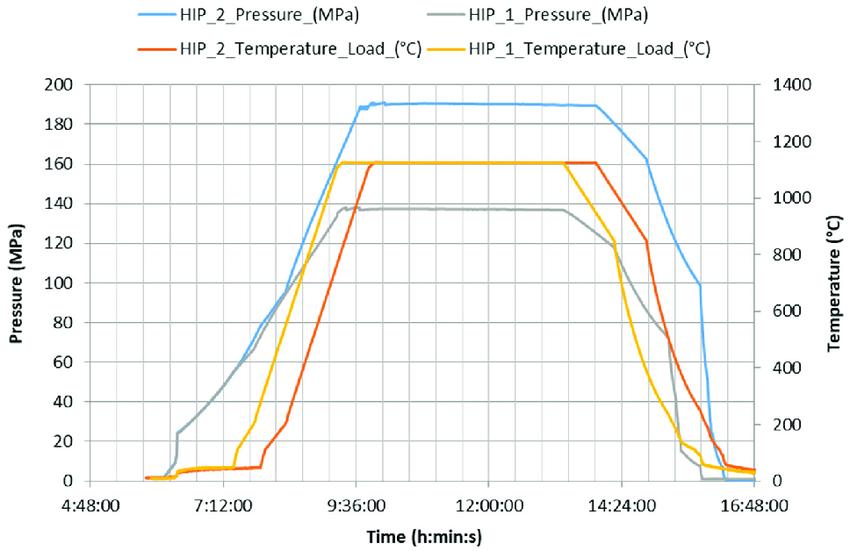
Temperature
As stated earlier, HIP requires very high temperatures. This is because the higher the temperature used for the process, the higher the degree of densification. The ideal temperature for hot isostatic pressing ranges from 1173 K to 2523 K. It is important to note that the temperature used for HIP should be below the melting point of the material being processed.
Pressure
Pressure is another factor that determines the degree of densification during HIP. The ideal pressure for hot isostatic pressing extends between 100 MPa to 200 MPa. Argon is usually used as the pressure medium.
Hold Time
This factor is just as important as the two factors mentioned above. However, the hold time required for a material to be appropriately densified is dependent on the thickness of the material. Generally, thick materials require a longer hold time than thin materials.
Applications of Hot Isostatic Pressing
Sputtering Target Fabrication
Hot isostatic pressing is an excellent process for preparing sputtering targets. The targets have less porosity and more density when they go through this process. The final product is usually microstructurally homogenous and ideal for sputtering. Hot isostatic pressing surpasses other processes which may be used to fabricate sputtering targets such as conventional hot pressing.
Aerospace
Hot isostatic pressing is commonly used in the aerospace industry. It is used to eliminate porosity from castings used in aircraft engines and components. In this way, it densifies these castings.
Diffusion Bonding
Hot isostatic pressing is used to join different materials. This can be achieved through cladding or even welding.
Medicine
HIP is used in making castings for surgical tools and medical implants such as braces. These tools made from hot isostatic pressing are of top quality and are usually long-lasting.
3D Printing
These days, 3D printing of metals is becoming more popular. When it is combined with hot isostatic pressing, the quality of the metals produced stands a chance against the quality of those produced from more conventional methods of manufacturing.
Sintering
Normally, sintering produces materials that contain varying degrees of porosity. However, hot isostatic pressing provides a solution to this problem. Materials sintered via HIP are usually stronger and more visually appealing.
Conclusion
Hot isostatic pressing is a highly beneficial process. It is presently used in various industries around the world and awareness about it keeps spreading. For more information about target manufacturing, please visit https://www.sputtertargets.net/.