What is Cold Isostatic Pressing (CIP)?
Cold isostatic pressing is a method of processing materials. It is quite similar to another process known as metal mold processing. CIP functions based on a principle proposed by Blaise Pascal. This principle is popularly known as Pascal’s law and it states that pressure applied in an enclosed fluid is transmitted in all directions throughout the fluid without any change in the magnitude of the pressure.
Cold isostatic pressing involves compacting powders by enclosing them in an elastomer mold. An elastomer mold is used because it has low resistance to deformation. Liquid pressure is then applied uniformly to the mold to compress it. At the end of the process, you are left with a highly compact solid. CIP can be used for plastics, graphite, powdered metallurgy, ceramics, sputtering targets and other materials.
Types of Cold Isostatic Pressing
There are two types of cold isostatic pressing currently recognized all over the world.
Wet Bag Technology
In this process, the powder is filled in a mold and sealed tightly. This occurs outside the pressure vessel. After filling the mold with powder, the mold is submerged in the pressure fluid within the pressure vessel. Then isostatic pressure is applied to the external surface of the mold, compressing the powder into a solid mass.
This process is not as common as the other type of cold isostatic pressing. There are over 3000 wet bag presses used all over the world today. These wet bags have sizes ranging from as small as 50mm to as big as 2000mm in diameter.
It takes from 5 to 30 minutes to process material using wet bag technology. Thus, it is relatively slow. However, high-volume pumps and improved loading mechanisms can go a long way in speeding up the process.
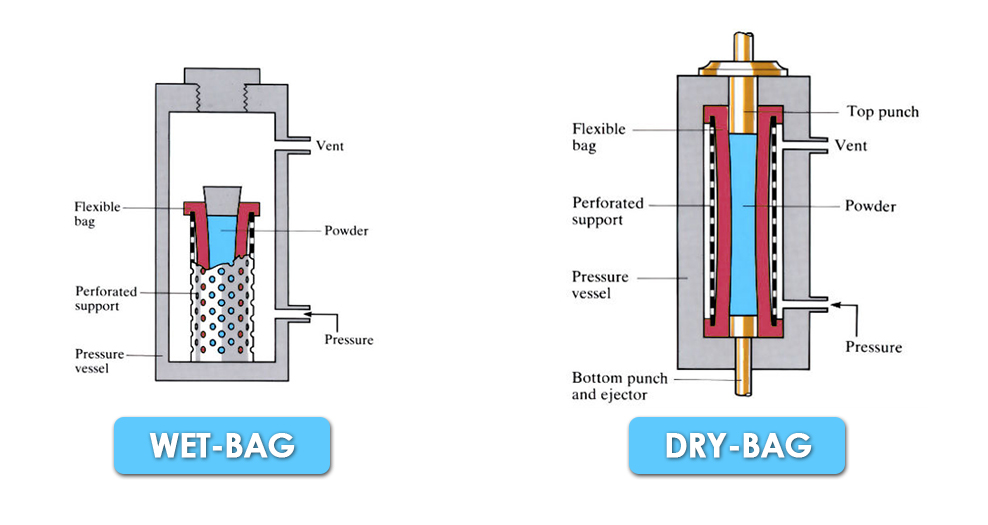
Dry Bag Technology
In this process, the mold is fixed in the pressure vessel. The powder is filled in the mold while it is still in the pressure vessel. After this, isostatic pressure from the pressure liquid is applied to the external surface of the mold, compressing the powder into a solid mass with a compact microstructure.
Dry bag technology is ideal for the mass production of materials. This process usually takes as little as 1 minute. It is way faster than wet bag technology.
Advantages of Cold Isostatic Pressing
Green Strength
Green strength is a term used to describe the ability of a molded material to withstand manipulation before it is completely hardened. Materials produced via cold isostatic pressing have high green strength. This means that such materials have a higher turnover as they can be sintered or machined faster than other materials.
Uniform Density
Cold isostatic pressing ensures that materials have a uniform density. This means that there will be uniform shrinkage when the material is going through other processes such as sintering. The uniform density can be attributed to the fact that the pressure used in CIP reaches every part of the material with equal magnitude.
Uniform Strength
Since the pressure used to compact the materials is equal in all directions, the material has uniform strength. Materials with uniform strength are usually more efficient than those without uniform strength.
Versatility
CIP can be used to produce difficult shapes which can not be produced by other methods. In addition, it can be used to produce large-sized materials. The only limitation to the size of materials produced by this method is the size of the pressure vessel.
Corrosion Resistance
Cold isostatic pressing improves the corrosion resistance of a material. Thus materials that undergo this process have a longer lifespan than most other materials.
Mechanical Properties
The mechanical properties of cold isostatic pressed materials are improved. Some of the properties improved include ductility and strength.
Advantages of Cold Isostatic Pressing
Powder Metallurgy
Cold isostatic pressing is used in powder metallurgy. It is used for the compacting step of powder metallurgy that comes just before the sintering step. In powder metallurgy, CIP is often used to produce complex shapes and dimensions.
Refractory Metals
CIP is used to produce refractory metals. They include tungsten, molybdenum, and tantalum. Tungsten, for example, is used to manufacture wires for filaments in the lamp industry. Generally, refractory metals have a high melting point and are resistant to wear and tear.
Sputtering Targets
Cold Isostatic Pressing (CIP) can press indium tin oxide (ITO) powder into large ceramic preforms, which are then sintered under certain conditions. This method can theoretically produce ceramic targets with a density of 95%.
Automobiles
Cold isostatic pressing is used in manufacturing automobile components. Some of these components include bearings and oil pump gears.
Sintering
Cold isostatic pressing usually comes right before sintering. Cold isostatic pressed products usually have a high green strength that allows them to be sintered faster than other materials.
Conclusion
More manufacturers are infusing cold isostatic pressing in the manufacturing process these days. From improved green strength to uniform density, cold isostatic pressing has several advantages over other similar processes. For more information about target manufacturing, please visit https://www.sputtertargets.net/.