Titanium alloys have been widely used in the aerospace industry. However, in recent years, although the aerospace industry is still the biggest market, the research and development direction of titanium alloys has shifted from the aerospace industry to the civilian industry. Titanium alloys applied for aerospace industry tend to have excellent performance but are EXPENSIVE. Therefore, researchers and manufacturers have done a lot of work to reduce the prices of titanium alloy.
Reduce the cost of raw materials
At present, most widely used titanium alloys contain expensive beta stabilizers (molybdenum, vanadium, chromium, etc.), which are too expensive for the civil industry. Therefore, from the viewpoint of raw materials, if it is replaced by other inexpensive materials, the cost can be greatly reduced. The most representative example is the use of iron at a price of $1.1/kg instead of vanadium at a price of $22/kg as a beta stabilizer. The United States and Japan have successively used vanadium-free titanium alloys for civil industrial applications. In addition, adding ruthenium or reducing high content of chromium in titanium alloy not only reduces the cost of raw materials, but also improves the corrosion resistance of the alloy.
Reduce the cost of processing and manufacturing
There are many reasons for the high cost of manufacturing titanium alloys, and the difficulty in processing titanium alloys is one of the most important reasons.
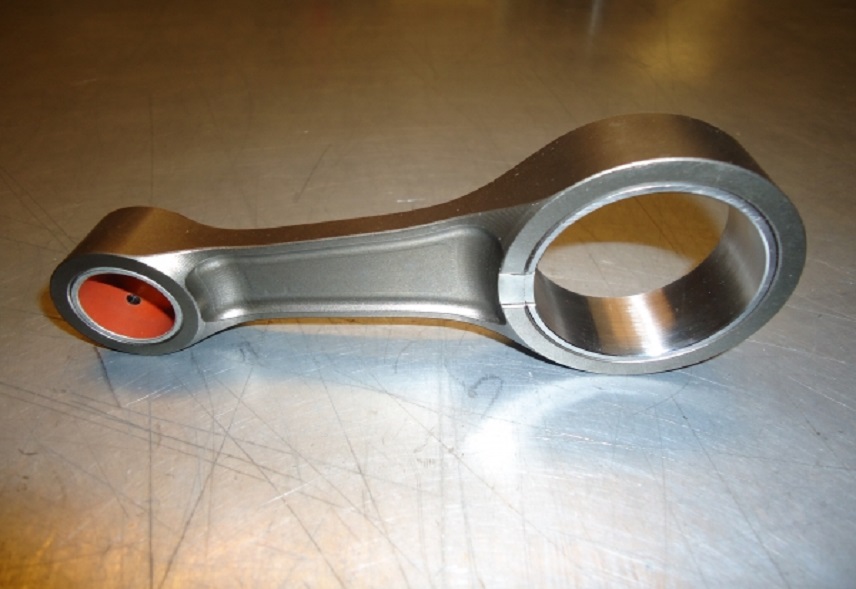
For example, in the manufacture of automobile connecting rods, the speed of processing titanium alloy is 50% slower than that of processing steel connecting rods. Therefore, the manufacturing cost of the former is much higher. More importantly, to produce the same amount of automotive connecting rods, the amount of titanium alloy used is twice that of steel. These factors have greatly increased the processing and manufacturing costs of titanium alloy products. There are several ways to reduce the processing cost of titanium alloys:
- Develop low-cost production processes (continuous casting, permanent casting, powder metallurgy, etc.). In recent years, the use of metal injection molding processes to manufacture titanium alloy products has attracted great interest because the process can directly produce titanium products with complex shapes without the need for melting, forging, machining, etc., thereby greatly reducing production costs.
- Develop new production processes such as the production of elemental powder or titanium.
- Use a more energy efficient reduction process, such as continuous reduction process.
Stanford Advanced Materials (SAM) Corporation is a global supplier of various sputtering targets such as metals, alloys, oxides, ceramic materials. Please visit our website https://www.sputtertargets.net/ for more information.