Introduction
When it comes to electron beam (e-beam) evaporation, the proper fill rate of a material in an e-beam crucible liner is an important consideration to ensure a successful deposition process. In this article, we will discuss what the fill rate is, why it is significant, and how to determine the proper fill rate for a specific material. Hope that you can have a better understanding of e-beam evaporation and the proper fill rate of the crucible liner.
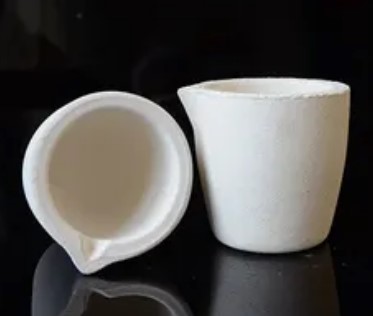
What Are E-beam Evaporation and the Fill Rate?
Electron beam evaporation is a physical vapor deposition method (PVD) that employs high-energy electron beams to melt aluminum, platinum, and other metals with high melting points.
During the deposition process, a variety of devices are utilized. Crucible liners are an essential part of filmmaking since they provide thermal isolation between the evaporation material and the crucible. Therefore, attention is required to the handling of the crucible liner.
The fill rate is such a crucial factor. It refers to the amount of material loaded into the e-beam crucible liner. It is expressed as a percentage of the total volume of the crucible liner. For example, if the crucible liner has a volume of 100 cubic centimeters and you load it with 80 cubic centimeters of material, the fill rate would be 80%.
A proper fill rate is important because it affects the uniformity of the deposited film. If the fill rate is too high, the material may not evaporate evenly, leading to a non-uniform film thickness. If the fill rate is too low, the e-beam may damage the crucible liner, leading to contamination of the material being deposited. Thus, much care and caution are needed in the evaporation process to avoid damaging the crucible liner.
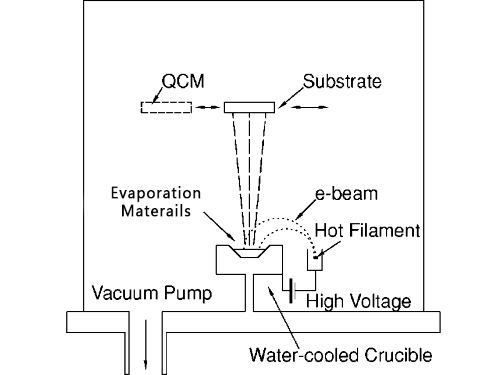
Related reading: Electron Beam Evaporation VS Thermal Evaporation
How to Determine the Proper Fill Rate?
The proper fill rate for a specific material depends on several factors, including the material’s melting point, boiling point, and thermal conductivity. Generally, a fill rate between 50% and 80% is recommended for most materials. However, certain materials may require a lower or higher fill rate to achieve optimal deposition results. For example, highly thermally conductive materials such as copper and silver may require higher fill rates (up to 90%) to ensure that they evaporate uniformly and deposit evenly on the substrate; Materials with low melting points such as indium and gallium may require lower fill rates (as low as 20%) to prevent overheating and evaporation before reaching the substrate.
To determine the proper fill rate, start by calculating the volume of material needed for your deposition process. This can be done by multiplying the desired film thickness by the surface area of the substrate being coated. Once you have the volume of material needed, calculate the appropriate fill rate by dividing the volume of material by the volume of the crucible liner.
It is also essential to note that the fill rate may need to be adjusted during the deposition process to ensure uniform film thickness, which can be done by gradually adding more material to the crucible liner as the deposition process progresses.
What Is the Proper Fill Rate of A Material in An E-Beam Crucible Liner?
- When considering the proper fill rate for material in an e-beam crucible liner, it is important to take into account the melt level of the evaporation material and its impact on the success of the operation. We recommend a proper fill rate of between ⅔ and ¾ full because we found the melt level of the evaporation material in the crucible directly affects the success of the operation.
- If we overfill the crucible, the material would spill over and there would be an electrical short, which would damage or crack the crucible. If there is too little material in the crucible, the evaporation rate would be seriously affected.
- Please remember to control the melt level above 30% so that the e-beam would not strike the bottom or walls of the crucible to avoid immediate cracking and breakage.
Conclusion
In a word, the proper fill rate of a material in an e-beam crucible liner is an important factor in achieving a uniform film thickness during deposition. The fill rate depends on several factors and should be calculated based on the material’s properties and the deposition process requirements. It is also important to monitor and adjust the fill rate during the deposition process to ensure optimal results.
Stanford Advanced Materials (SAM) is a reliable supplier of a range of crucibles and evaporation materials. We offer lab devices and advanced materials at an affordable price. For more information, please check our homepage.