Introduction
In the vast and intricate world of material science, the development and application of specialized materials are pivotal to technological advancement across various industries. Among these, evaporation materials hold a unique position due to their critical role in the fabrication of thin films, a foundational element in modern electronic, optical, and protective coatings. At the heart of this domain are nitrides and carbides, two classes of compounds distinguished by their exceptional properties and versatility. Nitrides, compounds of nitrogen with less electronegative elements, and carbides, compounds of carbon with more electropositive elements, are renowned for their hardness, thermal stability, and resistance to wear and corrosion. These characteristics not only make them indispensable in harsh operational environments, such as those encountered in aerospace and cutting tool applications but also highlight their potential in pioneering next-generation electronic and optical devices.
This article embarks on a detailed exploration of nitride and carbide evaporation materials, delving into their applications, properties, and the profound impact they promise for future technological innovations. By examining these materials’ foundational role in advancing display technologies and lighting solutions, we illuminate the path toward a brighter, more efficient future powered by the nuanced understanding and application of nitride and carbide materials.
Understanding Nitrides
Nitride evaporation materials represent a fascinating class of compounds that exhibit a wide range of chemical and physical properties, making them highly sought after for various industrial applications. Characterized by their combination with nitrogen, a relatively electronegative element, nitrides can be metallic, ionic, or covalent, each type presenting unique properties suited to specific uses.
Physical and Chemical Properties:
Nitrides are known for their exceptional hardness and high melting points, traits that render them ideal for applications requiring durability and thermal resistance. Many nitrides also exhibit significant thermal stability, maintaining their structural integrity even under extreme temperatures. This makes them excellent candidates for protective coatings in tools and components exposed to high wear and heat. Additionally, certain nitrides display semiconducting properties, opening avenues for their use in electronic devices.
Semiconducting Nitrides:
Gallium nitride (GaN) and aluminum nitride (AlN) are prime examples of semiconducting nitrides. GaN is pivotal in the production of LEDs and laser diodes, largely due to its wide bandgap, which allows for operation at higher temperatures and voltages with increased efficiency. AlN is similarly valuable, offering high thermal conductivity and electrical insulation, making it ideal for substrates and insulators in electronic applications.
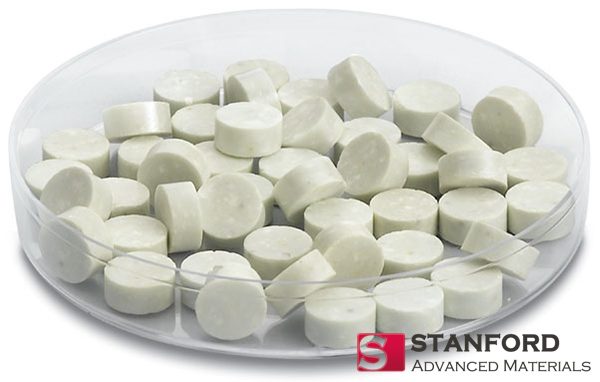
Applications in Industry:
The broad applicability of nitrides spans from cutting tools and protective coatings, leveraging their hardness and thermal resistance, to advanced electronics, where their semiconducting properties are crucial. In the aerospace industry, nitrides are employed in protective coatings for engine components, offering resistance to high temperatures and corrosion. The automotive industry benefits from nitride coatings in enhancing the longevity and performance of engine parts.
The versatility of nitrides, underpinned by their diverse chemical and physical properties, establishes them as indispensable materials in both traditional and cutting-edge technologies. Their continued development and application promise to drive innovation across a spectrum of industries, from manufacturing to electronics.
Understanding Carbides
Carbide evaporation materials are compounds characterized by the presence of carbon atoms bonded to less electronegative elements, forming predominantly covalent structures. This class of materials is celebrated for its remarkable hardness, high melting points, and excellent thermal and electrical conductivity, making carbides invaluable across a myriad of applications, especially where extreme conditions are encountered.
Physical and Chemical Properties:
The defining feature of carbides is their exceptional hardness, rivaled only by diamonds in some instances. This characteristic, combined with their ability to withstand high temperatures, positions carbides as ideal materials for cutting tools and abrasives used in manufacturing and engineering sectors. Moreover, certain carbides, such as silicon carbide (SiC), exhibit semiconducting properties that have been harnessed in advanced electronic and optical devices.
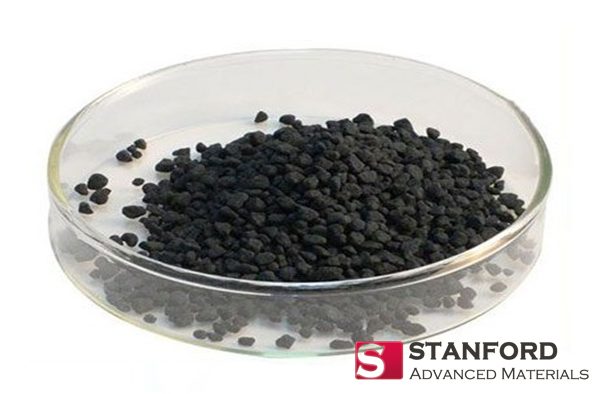
Semiconducting Carbides:
Silicon carbide stands out for its application in power electronics, where it enables devices to operate at higher voltages and temperatures with improved efficiency compared to silicon-based counterparts. Its thermal conductivity and resistance to thermal shock also make SiC an excellent material for high-temperature applications, such as aerospace and automotive components.
Applications in Industry:
The versatility of carbides extends to their use in protective coatings, where they offer unmatched resistance to wear, corrosion, and thermal degradation. This makes them ideal for enhancing the durability and performance of mechanical parts subjected to harsh operational environments. Additionally, carbides find applications in the nuclear industry, where their high neutron absorption capabilities are utilized.
The broad spectrum of carbides’ applications underscores their significance in modern technology and industry. From enhancing the durability of tools to enabling the next generation of semiconductors, carbides continue to play a pivotal role in driving technological advancements and improving the efficiency and longevity of various components and systems.
Evaporation Process Overview
The evaporation process, particularly for advanced materials like nitrides and carbides, is a cornerstone technique in the deposition of thin films, crucial for various technological applications. This process involves the transformation of a solid material into vapor, which then condenses onto a substrate to form a uniform coating. Achieving high-quality coatings of nitrides and carbides through evaporation requires a nuanced understanding of the materials’ properties and the optimization of process parameters.
Vacuum Environment:
A critical aspect of the evaporation process is the maintenance of a vacuum environment. This ensures that the vaporized particles can travel to the substrate without interacting with other particles or contaminants in the air, which could compromise the purity and quality of the deposited film. A vacuum environment also aids in controlling the evaporation rate and temperature, essential factors for materials with high melting points like many nitrides and carbides.
Temperature Control:
The evaporation of nitrides and carbides poses a unique challenge due to their high melting points. Precise temperature control is paramount to vaporize these materials effectively without degrading their properties. Advanced heating techniques, such as electron beam (e-beam) evaporation, are often employed to achieve the temperatures necessary for the evaporation of these robust materials.
Challenges Specific to Nitride and Carbide Evaporation:
One of the primary challenges in the evaporation of nitrides and carbides is the potential for chemical decomposition at high temperatures, which can alter the stoichiometry of the resulting film. Additionally, the high energy required for evaporation can lead to challenges in achieving uniform film thickness and composition across the substrate.
Innovations in Deposition Techniques:
To overcome these challenges, innovations in deposition techniques, such as pulsed laser deposition (PLD) and chemical vapor deposition (CVD), have been developed. These methods offer greater control over the film’s properties, allowing for the deposition of complex nitride and carbide films with precise compositional and structural characteristics.
The evaporation process for nitrides and carbides is a sophisticated endeavor that demands a deep understanding of material science and engineering principles. The ability to navigate the intricacies of this process is critical for leveraging the unique properties of nitrides and carbides in thin-film applications, pushing the boundaries of what is achievable in advanced coatings and electronic devices.
Applications of Nitrides and Carbides
Nitride Applications
Nitrides have carved out a significant niche across several high-tech industries, thanks to their unique blend of physical and chemical properties. In the aerospace sector, aluminum nitride (AlN) and silicon nitride (Si₃N₄) are particularly prized for their thermal stability and resistance to wear, making them ideal for components exposed to extreme conditions, such as turbine blades and engine parts. These materials offer enhanced durability and efficiency, critical in aerospace applications where reliability is paramount.
In electronics, gallium nitride (GaN) stands out as a transformative semiconductor material, enabling the development of high-power and high-frequency devices, including transistors and diodes. Its superior efficiency and thermal performance have led to significant advancements in communication technology, renewable energy systems, and fast-charging solutions. GaN’s ability to operate at higher temperatures and voltages than traditional silicon semiconductors also opens up new possibilities in designing compact, energy-efficient power converters.
The biomedical field benefits from the biocompatibility and mechanical strength of certain nitrides, such as silicon nitride, which finds applications in orthopedic implants and dental restorations. Its resistance to bacterial colonization and excellent compatibility with human tissue make it a promising material for medical devices and prosthetics.
Carbide Applications
Carbides are renowned for their exceptional hardness and resistance to wear, making them indispensable in manufacturing and engineering. Tungsten carbide, for instance, is a staple in the production of cutting and drilling tools, offering unmatched durability and precision. Its ability to maintain sharpness and strength under high-stress conditions revolutionizes machining processes, enhancing productivity and reducing downtime.
In the realm of semiconductors, silicon carbide (SiC) emerges as a key material in high-voltage applications. Its use in diodes, transistors, and power modules enhances the efficiency of electric vehicles and renewable energy systems by enabling higher voltage operations and superior thermal management. This contributes to the development of greener, more sustainable energy solutions.
Protective coatings made from carbides, such as titanium carbide (TiC) and chromium carbide (Cr₃C₂), extend the life of mechanical parts by safeguarding against wear, corrosion, and high temperatures. Applied to tools, aerospace components, and even automotive parts, these coatings ensure reliability and performance in demanding operational environments.
Conclusion
The exploration of nitride and carbide evaporation materials unveils a realm where innovation meets necessity, propelling advancements across a spectrum of industries. From aerospace to electronics, and cutting-edge medical devices to everyday tools, the unique properties of these materials—harnessed through sophisticated evaporation processes—have paved the way for technological leaps that were once beyond imagination. This journey through the applications and properties of nitrides and carbides underscores not just their current significance but also the potential they hold for future innovations. As research continues to delve deeper into the capabilities and potential new uses of these materials, their role in technological advancement is set to expand even further. The continuous push for innovation, supported by advancements in material science, promises to unlock even more applications, enhancing the efficiency, durability, and performance of the next generation of technological solutions.
Click to Inquiry High Quality Evaporation Materials